Enhanced component performance through subsurface conditioning in BTA deep hole drilling
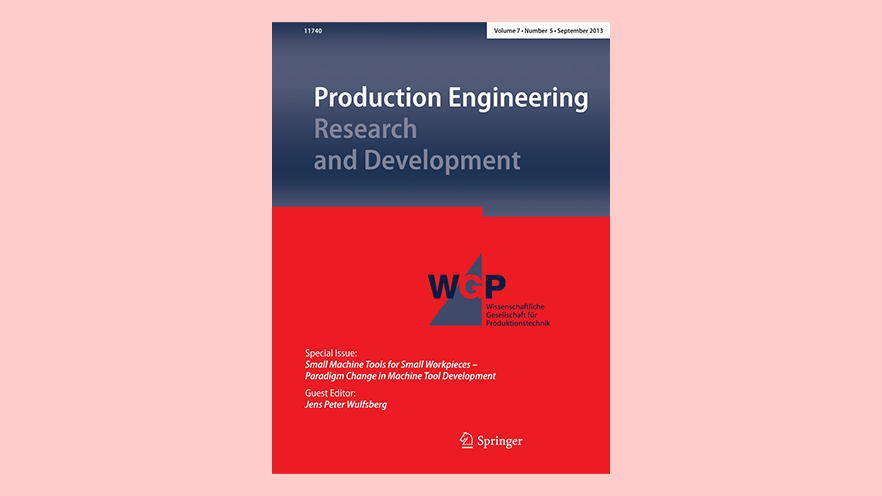
Explore how subsurface conditioning in BTA deep hole drilling enhances component performance. Through the analysis of drilling factors and advanced detection methods, researchers strive to enhance surface integrity and ensure the reliability of critical components.
Scientific articles
|
19. 02. 2024
|
by Production Engineering
Product
Technology
Related articles
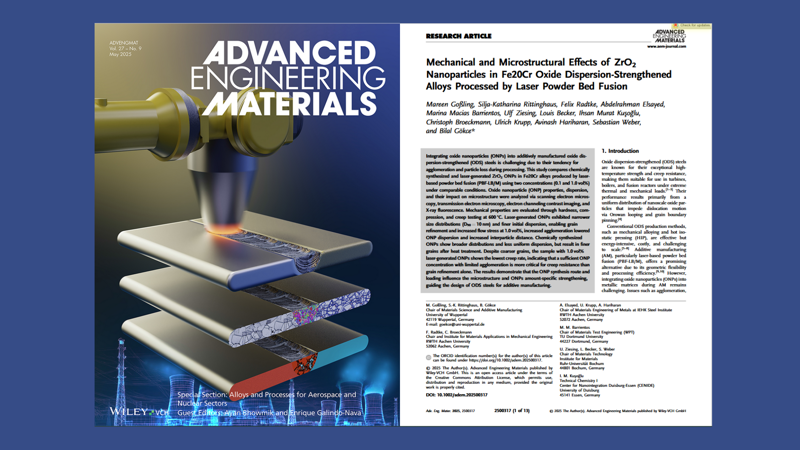
Scientific articles
|
21. 05. 2025
|
by Advanced Engineering Materials
ZrO2 Nanoparticles in Fe20Cr Oxide Dispersion-Strengthened Alloys Processed by Laser Powder Bed Fusion
Material Science
Technology
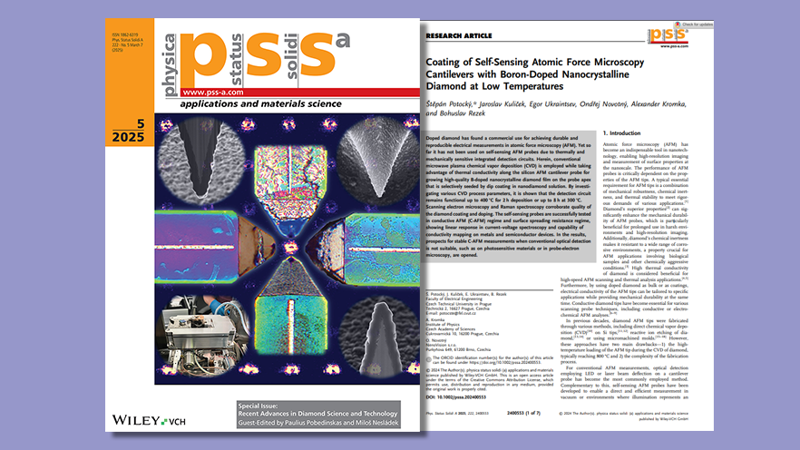
Scientific articles
|
12. 03. 2025
|
by Phys. Status Solidi A
AFM-in-SEM LiteScope on the Cover of a Key Study on Diamond-Coated Probes
Material Science
Technology
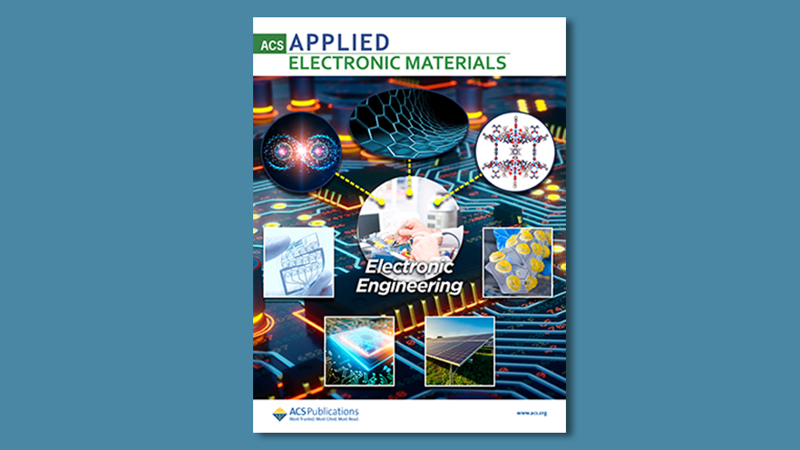
Scientific articles
|
17. 12. 2024
|
by ACS Applied Electronic Materials
Impact of Electron Irradiation on WS2 Nanotube Devices
Material Science
Technology
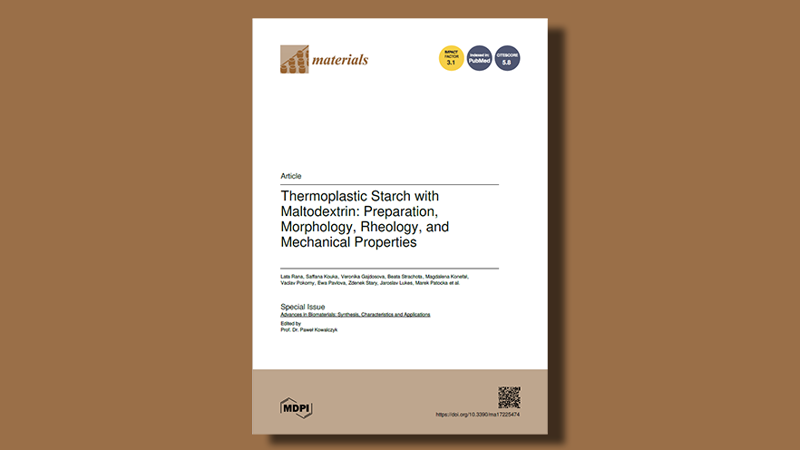
Scientific articles
|
18. 11. 2024
|
by Materials
Enhancing Thermoplastic Starch with Maltodextrin: Key Properties and Performance Insights
Material Science
Technology
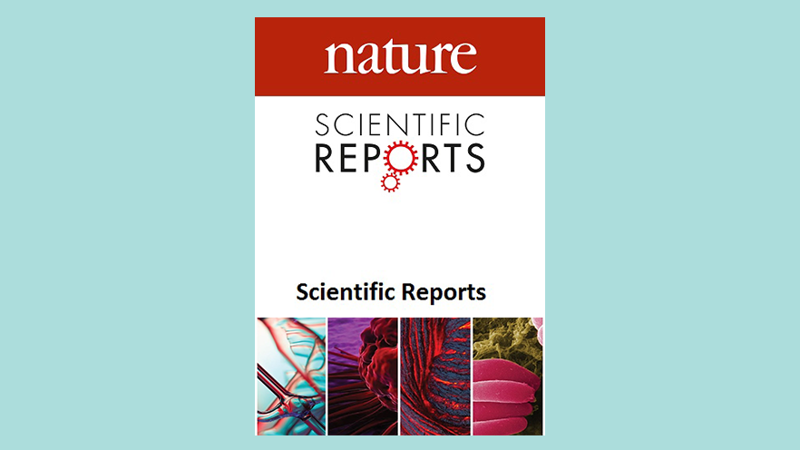
Scientific articles
|
12. 08. 2024
|
by Scientific Reports
3D Surface Roughness Measurement of Core–Shell Microparticles
Product
Technology